Lift safety is extremely important! In this Lift Safety Guide, we’ll explore the importance and history of lift safety in detail. From installation to maintenance, we will also examine the safety features keeping our lifts in such good condition today, and why you should consider investing in quality, comprehensive maintenance contracts for your own new – or existing – lift.
Are Lifts Safe?
The big question is this: are lifts really safe? Many of us may have heard stories about lifts breaking down or needing repair and developed concerns about them as a result. Fortunately, LOLER Regulations demand that lifting equipment must be of adequate strength and stability, reducing the risk of harm to occupants and the surrounding property. These regulations exist to lower the risk of accidents, which were, unfortunately, well known prior to the careful use of lifting equipment!
Human and power failures were equally dangerous in the past, and companies like ours at Sheridan Lifts do our utmost to prevent these incidents. With our LOLER certification, (which any reputable lift company should have), we ensure business owners meet the safety regulations the regulatory body demands of them.
Don’t forget, lifts undergo frequent inspections too. Inspection by an authorised and competent person – a professional who understands risk assessment well, and knows how to conduct routine safety checks – makes our lifts safer than ever. This is exactly what we do at Sheridan Lifts.
We also have a variety of vital safety features in place that provide valuable security to all lifting equipment we work with.
Lift Safety Features
Basic designs, more often than not, include a safety valve. There are different types of safety valve, but a conventional safety valve closely follows any changes in the backpressure to the valve. Simply put, the valve will sync with the maximum load pressure of a lift, so when an elevator overloads, the safety valve opens. Therefore the lift moves only after a part of the heavy load is unloaded!
Damage to valuable components is prevented, helping to reduce the chance of accidents. Similarly, with a balanced safety relief valve, this valve minimises the effects of backpressure on the operation of the valve, ensuring the lift and its components are always protected from harm.
Safety valves aren’t the only important safety feature of a lift, however! Lifts have an essential closing device to avoid accidental entry into the hoistway. The lift simply won’t open unless the main table has reached the desired floor – quite a neat trick of technology, and one that also guarantees elevators remain a safe environment for employees and customers alike.
For your peace of mind, communications devices are often contained within a lift as well, ensuring contact can be established with safety personnel in the unlikely event a lift stops or jams before the floor is reached.
A major safety feature of an elevator is the actual material it’s made out of too. With a cast steel body, made with durable stainless and carbon steel materials, very little can damage or weaken the integrity of the lift itself.
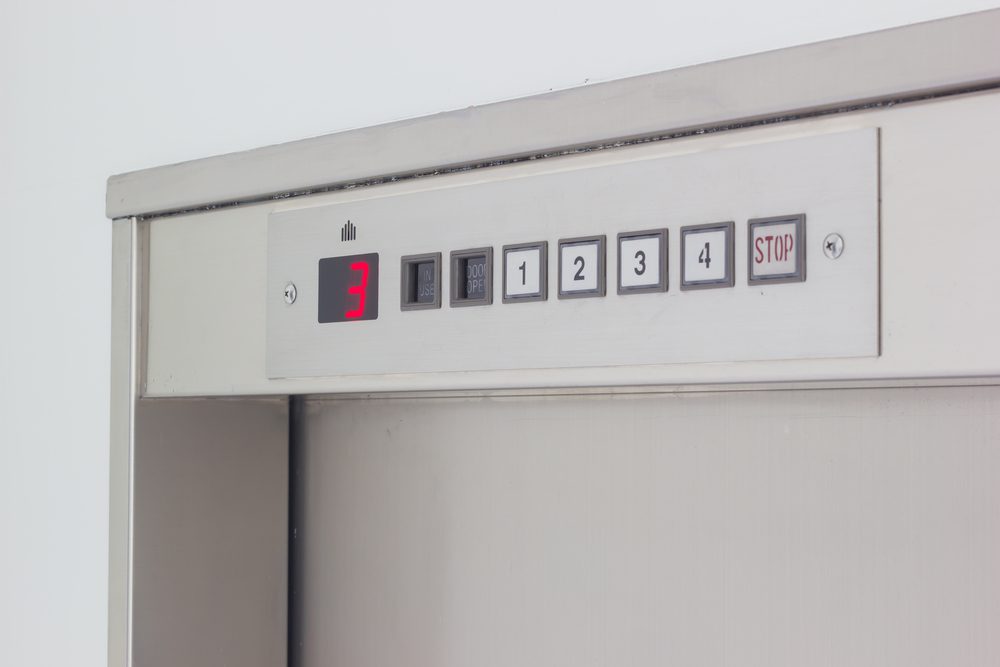
LOLER Regulations Explained
You may recall our mention of LOLER Regulations previously. Here, we’re going to go into a little more detail about what these regulations actually stand for and refer to.
LOLER is the abbreviation for ‘Lifting Operations and Lifting Equipment Regulations.’ To sum the LOLER Regulations up, they dictate what owners should do to keep their lifting equipment safe. This equipment includes everything from passenger lifts to telehandlers, cranes and hoists. Some of the regulations that must be followed include:
- Hiring competent and qualified lift operators
- Only using lifting equipment for its intended use
- Ensuring maintenance checks and inspections are carried out regularly
- Making sure that inspections are carried out before any lift is put into action
LOLER regulations are important because they ensure people keep a close eye on the installation, operation and use of their lifting equipment. Unchecked, this lifting equipment could be overloaded or fall into disrepair. By having strict regulations, we are closer to avoiding dangerous incidents completely.
What is in a Lift Maintenance Checklist?
At Sheridan Lifts, we’re experts in the area of lift maintenance, so we’re qualified to tell you about lift maintenance and what should be in your passenger lift inspection checklist!
An inspection checklist should encompass both the inside and the outside of the lift, including the cabin, machine room, shaft and pit. In our regular inspections of a lift cabin, our expert lift engineers cover the following areas:
- Exterior call button lights
- Lift door panels and clearance
- Firefighter lift controls
- Smooth, accurate acceleration, deceleration and levelling when the lift is operated
- Lift doors mustn’t slam when closing
- Door restrictor
- Position indicators and lights
- Wear and tear in the lift interior
Elsewhere, we may remove debris from the top of the cabin, check the cabling for any wear or damage, and ensure guide rails and levelling devices are in good condition. It’s also important to check all electrical components in the machine room are functioning as they should!
The Importance of Proper Lift Maintenance
Regular lift maintenance isn’t an option, but a necessity. Without regular maintenance, not only do owners run the risk of their lift breaking down, they also may put employees and customers in danger.
For example, faulty components when left to wear and tear can jam your lift, potentially with people inside. There’s no stronger, more efficient preventative measure to accidents than regular and proper lift maintenance. Don’t wait till repairs are needed!
Legally, any lift that carries people must be inspected at least every six months and any lift that carries goods must be inspected annually.
Investing in a long-term maintenance contract for all of the new and existing lifts you own ensures you don’t miss a single inspection, keeping your lifts in the best condition they can be! Here, the money you spend on a long-term contract is repaid tenfold when you don’t have to shell out thousands on costly lift repairs. Sheridan Lift maintenance contracts can cater to your business and the lifting equipment within, saving you money and ensuring your building runs as usual.
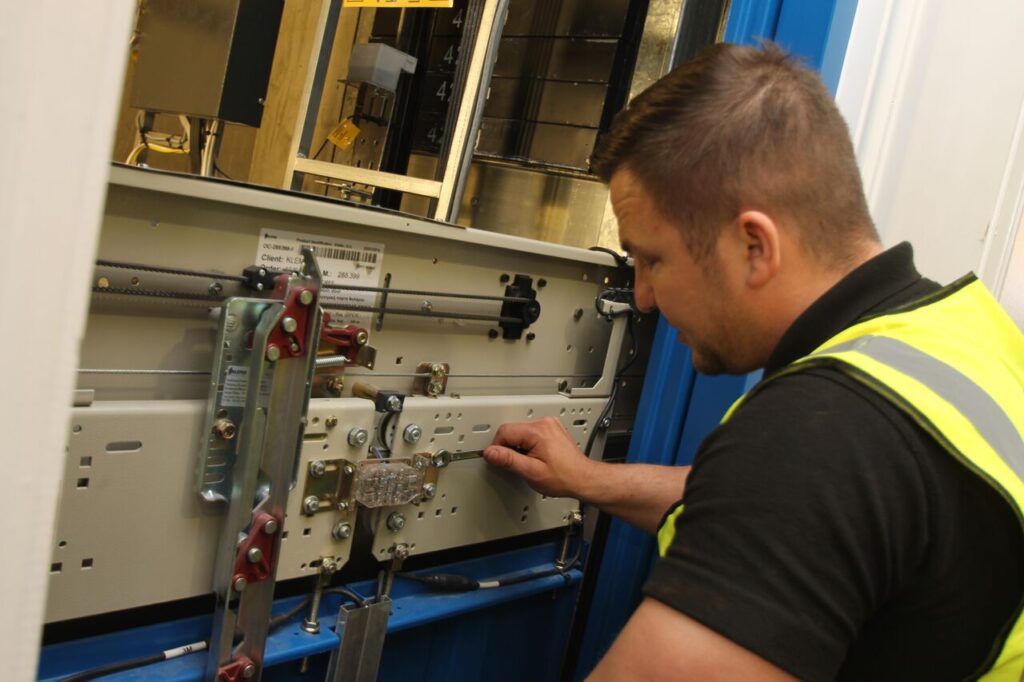
Lift Maintenance with Sheridan Lifts
We have a great variety of lift maintenance packages for our customers. Choose from our three bespoke packages – tailored to be as accessible or as unique as you need them to be.
Sheridan Standard
If you only have one or two lifts on site, few floors to cover and low usage rates, Sheridan’s Standard package is recommended. Here, we can provide 4, 6 or 12 service visits a year depending on your needs, to guarantee your lifts remain legally compliant and functional.
Callouts and parts are excluded, but our 24-hour helpline will always be available to you.
Sheridan Comprehensive
As the name Comprehensive suggests, this package involves all-inclusive lift maintenance. Here, we carry out 6 or 12 service visits, lending the services of our capable team of lift engineers! Any event, including parts needed for repair, is covered up to £350.
Sheridan Premium
Sheridan Premium is the best lift maintenance we have to offer. Customers can expect 4, 6 or 12 service visits in their contract, with breakdown callouts during working hours included. We work closely with you to develop additional bespoke packages for your lifting equipment, ensuring you’re getting the best service possible from our Sheridan team.
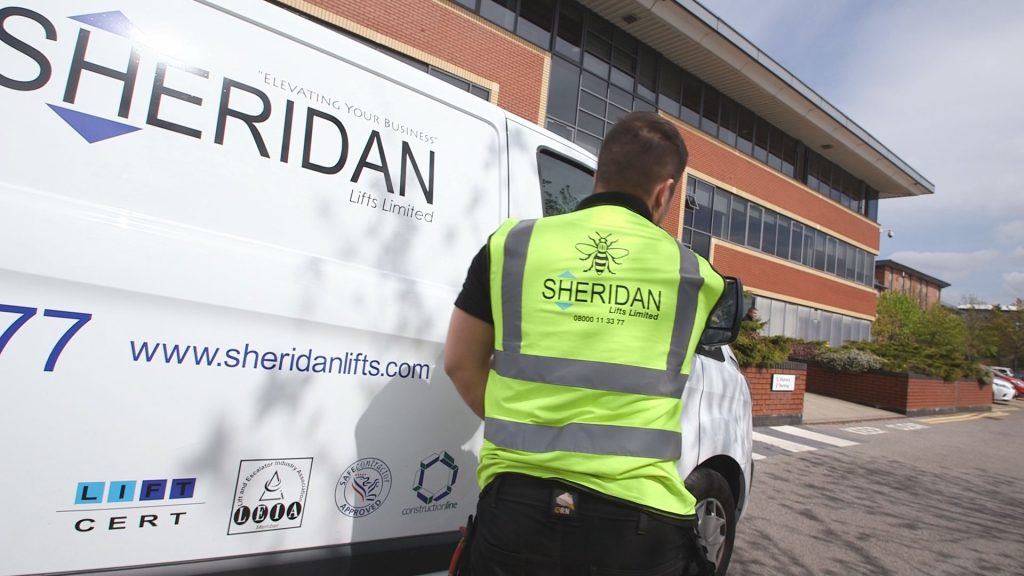
Make Sure Your Lifts are Safe with Sheridan Lifts
As the UK’s largest independent lift company, we have over 40 years of experience in lift safety, installation and maintenance. We take care of your lift throughout the year, happily installing new lift equipment whenever needed! Don’t hesitate to arrange your very own lift maintenance contract with us, or connect with us regarding any lift-related enquiries. Contact us today.