As an architect, building owner or site manager, you have a legal duty of care to ensure the safety of your staff, customers, residents and visitors when they use your facilities.
This is the case for every aspect of your building, but if you have – or are looking to install – lifts on your property, there are guidelines and regulations in place to make sure that all users stay safe.
In this guide, we’ll talk about several different regulations that all lifts and vertical transport have to adhere to, and why it’s so important that they are followed in all kinds of projects.
Of course, accidents can still happen no matter how careful you are. However, these regulations, among many others, have been put in place over time to learn from past accidents and help prevent future ones.
To learn more about lift regulations and the key considerations that you should be aware of when carrying out any new lift installation or building project, keep reading or get in touch with the team at Sheridan Lifts! We have decades of experience in lift installation and have seen the introduction of many of these new pieces of legislation. We’re passionate about staying ahead of the industry, and that includes being up-to-date on all lift industry safety regulations and guidance on accessibility issues, so you can feel confident your project is in safe hands with us.
PUWER
In accordance with the Provision and Use of Work Equipment Regulations (PUWER), any equipment used by employees at work must be controlled or prevented from posing a health and safety risk to the individuals. This extends to lifts and lifting equipment as well.
Under PUWER regulations, all equipment used by workers must be:
- Suitable for the intended use
- Safe for use (as per LOLER requirements, more on that in a moment!)
- Used only by trained people who are familiar with the equipment
- Accompanied by suitable safety measures such as signage, protective devices/clothing, markings and warnings, if applicable
For most businesses, remaining PUWER compliant when it comes to their lifts is very simple, and just requires a regular lift maintenance contract. Regular lift maintenance and lift servicing measures allow you to ensure the safety of your lifts on a regular basis, and will save you time and money calling out and fixing repairs which could have been avoided!
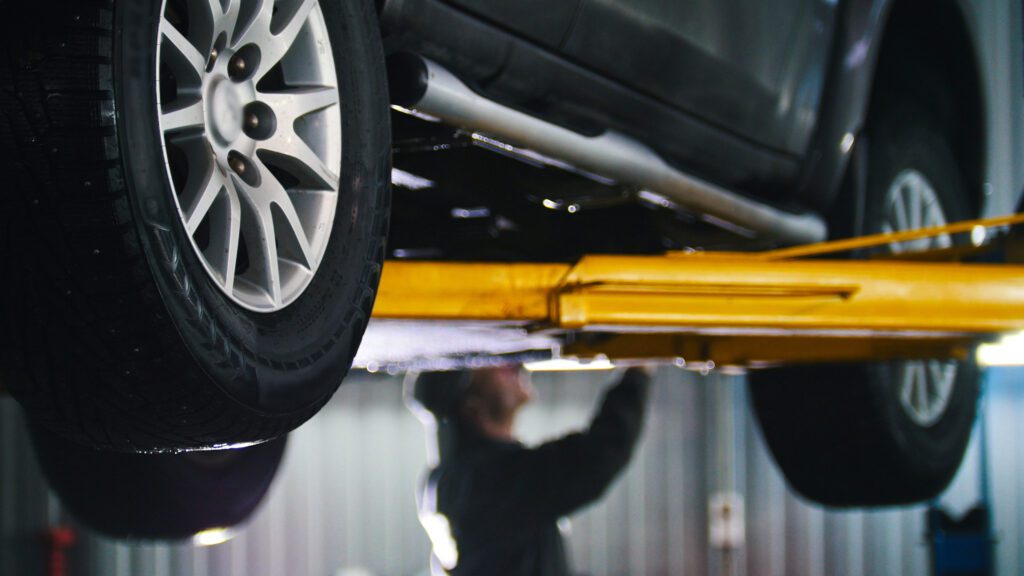
LOLER
It is the responsibility of people and companies who own, operate or have control over lifting equipment to comply with the Lifting Operations and Lifting Equipment Regulations 1998 (LOLER). LOLER regulations are similar to PUWER but are more specific to lifts and vertical transport.
LOLER regulations require that all lifts and lifting equipment provided is:
- Marked clearly to indicate safe working loads and strong & stable enough for its specific use
- To minimise any risks, the equipment must be positioned and installed in a safe manner
- Used safely by its operators, without overloading or misusing the lift
- Examined thoroughly and, where necessary, inspected by competent individuals.
Compliance with LOLER is through examinations of lifts and lift shafts in addition to regular servicing. Both regular examinations and servicing are always documented by Sheridan Lifts engineers in service reports, to show compliance and protect your organisation in case of an accident.
LOLER is an incredibly important set of regulations for those in the lift industry, so it’s important when choosing a reputable lift provider for your vertical circulation, that they have a strong understanding of these regulations. To learn more, take a look at our in-depth Lift Safety Guide, or get in touch with our expert team!
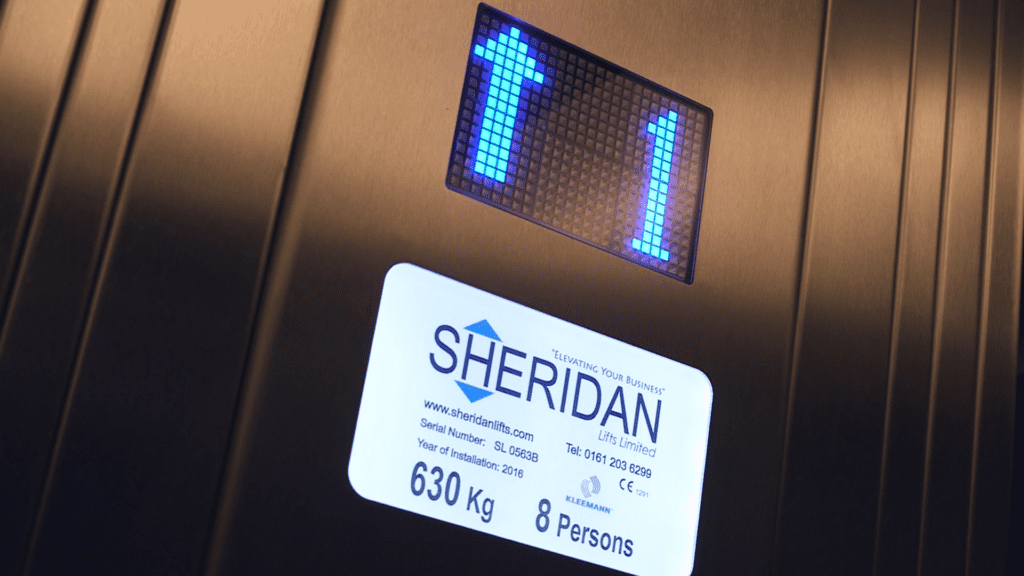
Manual Handling Regulations
On the surface, manual handling regulations aren’t actually directly related to lift installation. However, they are an essential consideration, particularly when it comes to building or installing goods lifts, service lifts, and dumbwaiter lifts. Health and Safety Executive (HSE) or local authorities report more than a third of all work-related illnesses each year to be caused by manual handling – transporting or supporting loads by hand or using bodily force.
For this reason, Manual Handling Regulations are in place to protect your team, staff or building users from potential injuries caused by “inappropriate manual handling”. But what does that have to do with lifts?
Manual handling covers all kinds of physical movement of goods (these can be objects, people or animals, depending on the context), such as:
- Lifting and picking up goods
- Putting down goods
- Pushing or pulling loads
- Carrying or moving loads
If something needs to be moved by hand or using bodily force, it’ll come under Manual Handling.
The HSE recommends that to reduce the risk of injury and improve the safety of persons in any work environment, the best solution is to remove the need for manual handling where practical. Organisations can do this with the help of automation technology, including conveyors, chutes, pallet trucks, electric or hand-powered hoists, or a goods or goods passenger lift.
The law requires you to protect your employees from unnecessary manual handling injuries. By failing to provide an efficient method for moving goods in the event of an accident or injury, you would be deemed responsible by the health and safety executive. This is why lifts are a vital part of ensuring user safety and protecting your organisation.
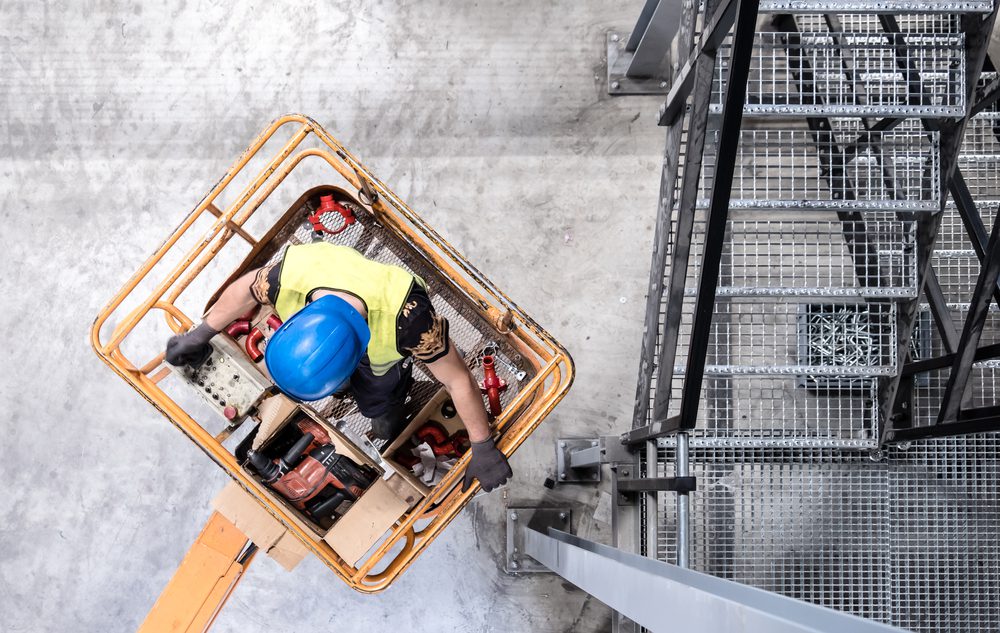
Part M of the Building Regulations Approved Document M
The Building Regulations Approved Document M (Part M) gives direction on lifts in all types of buildings, stating that reasonable provisions must be made for people to access and use the building’s facilities, including disabled people and people with impaired mobility.
These regulations are primarily focused on accessibility and creating spaces which as many users as possible can interact with. Part M is closely related to the Equality Act 2010, however, they are not the same piece of legislation.
What is Part M?
While the Equality Act sets out the legal need to make accommodations to improve the accessibility of a building, it doesn’t detail any of the exact requirements or describe what a suitable form of access looks like. That’s where Part M comes in, making it an incredibly valuable reference point for employers, building owners and other service providers.
In the latest Building Regulations Approved Document M, there are three key sections:
- Volume 1 – This volume sets out the essential safety requirements and relevant requirements for accessibility for dwellings/residential buildings.
- Volume 2 – This volume sets out the essential safety requirements and relevant requirements for accessibility or all other building types.
- Section 3 – Section 3 is slightly different, as it is the part of the document that sets the objectives that Volumes 1 and 2 are aiming to achieve.
The following is the key objective set out in Section 3:
“For all people to travel vertically and horizontally within buildings conveniently and without discomfort to make use of all relevant facilities. This objective relates in the main, but not exclusively, to the provision of sufficient space for wheelchair manoeuvre and design features that make it possible for people to travel independently within buildings.”
Translation: to make buildings and building travel accessible to as many people as possible, including wheelchair users!
When we consider Part M regulations for lift installations, there are several factors to examine, including the type of lift that is most suitable and any additional or specific requirements for these lifts.
For most buildings, a conventional passenger lift of appropriate size (the Part M minimum is 1100mm x 1400mm, or a standard 8-person lift) is the most commonly recommended lift type. However, Part M does take into account the fact that this isn’t always possible, and in existing buildings or exceptional circumstances, another option may be more practical.
The second option recommended by Part M where a traditional passenger lift can’t be used is a vertical lifting platform/enclosed platform lift. In exceptional circumstances (almost always in existing buildings), a wheelchair platform stairlift/open platform lift may be an option, as long as it doesn’t interfere with any pre-existing emergency escape routes.
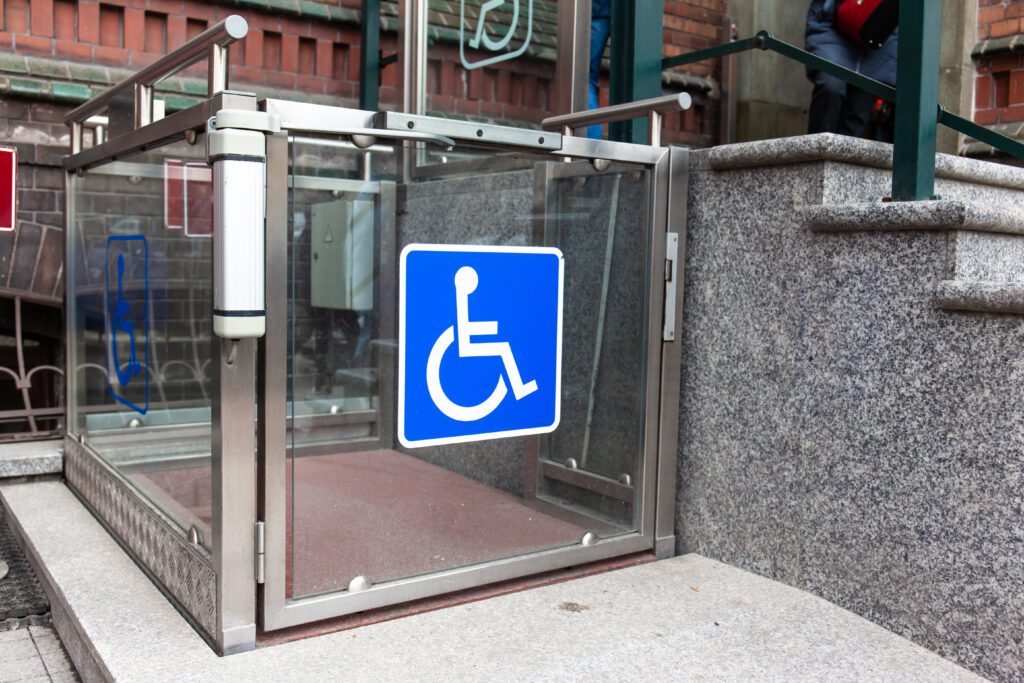
Whichever type of lift is chosen for vertical transportation in your building, several design considerations can improve access for persons with impairments that might not affect their mobility, but are still required to install a compliant lift. There is a broad range of considerations required, but some may include:
- The provision of audio and visual information in the lift lets users with additional accessibility requirements know when and where the lift is stopping.
- Making lifts large enough to suit the needs of the building, as well as to suit the needs of lift users with additional accessibility needs – the minimum size of lifts should accommodate both a wheelchair user and a passenger, with manoeuvring space for both parties.
- Ensuring that the landing call buttons and internal lift controls that summon and direct both traditional passenger lifts and disabled access lifts are within reaching distance for all users.
- Including emergency lighting and emergency communication systems that are accessible to all users.
- Include handrails.
It’s worth noting that Part M is only applicable in England and Wales – Scotland has its own version of Part M, though they are practically very similar.
At Sheridan Lifts, we have extensive experience in building and installing Part M compliant lifts (sometimes known as ‘Part M lifts’). You can be confident that both your standard and bespoke lift projects will be compliant with all the relevant lift regulations when you work with our team of experts.
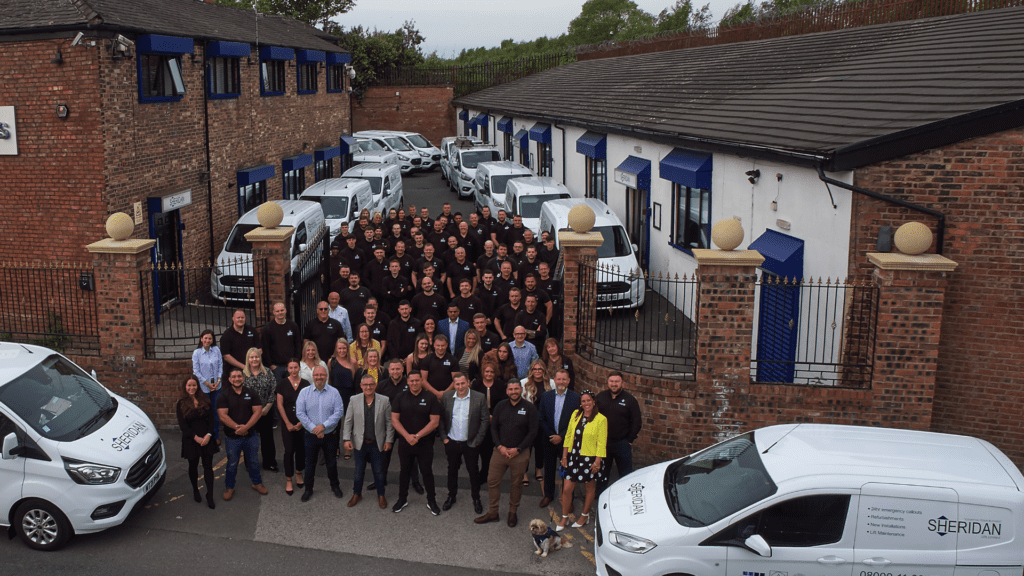
Learn More About Lift Compliance and Lift Regulations
Feel free to reach out to our expert team if you’d like to learn more about Sheridan Lifts, our lift design, installation, and ongoing lift maintenance services! Let us know what your project needs are and we’ll be happy to share our expertise and insight with you. We can offer detailed guidance, inspection reports, advice on lift access and circulation of people, and clarity on the relevant standards and requirements your lifts need to be compliant with!